Human-machine co-working is a crucial point for creating socially sustainable manufacturing. Focus Areas (Flagships) - EIT Manufacturing.
Very often with the advancements dictated by Industry 4.0, traditional production planners are able to manage machine planning very precisely, while the human resource is often considered accessory.
AIRP for Manufacturing overcomes this approach, by providing a pluggable service delivering custom strategies to solve complex resource planning. The support can integrate existing Manufacturing Execution Systems (MES), to extend their capabilities with cloud-based scenario modelling designed to effectively allocate resource production machinery according to the MES production cycle, considering a wide range of options that, for their nature or technologies, most MES do not currently consider when allocating human resources.
Below is a preliminary list of requirements from manufacturing companies we are helping with the tool:
- Specialisation of operators on the machine: The machine operator is linked to the type of processing (moulding, assembly, etc.)
- Machine start-up times: The availability of the resources could delay the subsequent phases.
- Time Requirements: Resources need to take a mandatory break every 4 hours, regardless of the type of machinery it operates on.
- Priority and lead time.
- Composition of shifts and expected roles (Shift Manager, Tool Operators, Supervisor, Fire Prevention, First Aid).
- Number of operators per shift: The number of operators tends to be balanced to efficiency and utilisation.
- Physical abilities.
All the constraints above are oftentimes managed outside the production scheduler software, oftentimes even for a company with 50 employees, facing significant limitations in identifying optimisation patterns and new strategies for allocating resources.
The solution gives organisations a better overview of their workforce, skills, and availabilities and predicts future bottlenecks, training needs and critical profiles according to manufacturing demands.
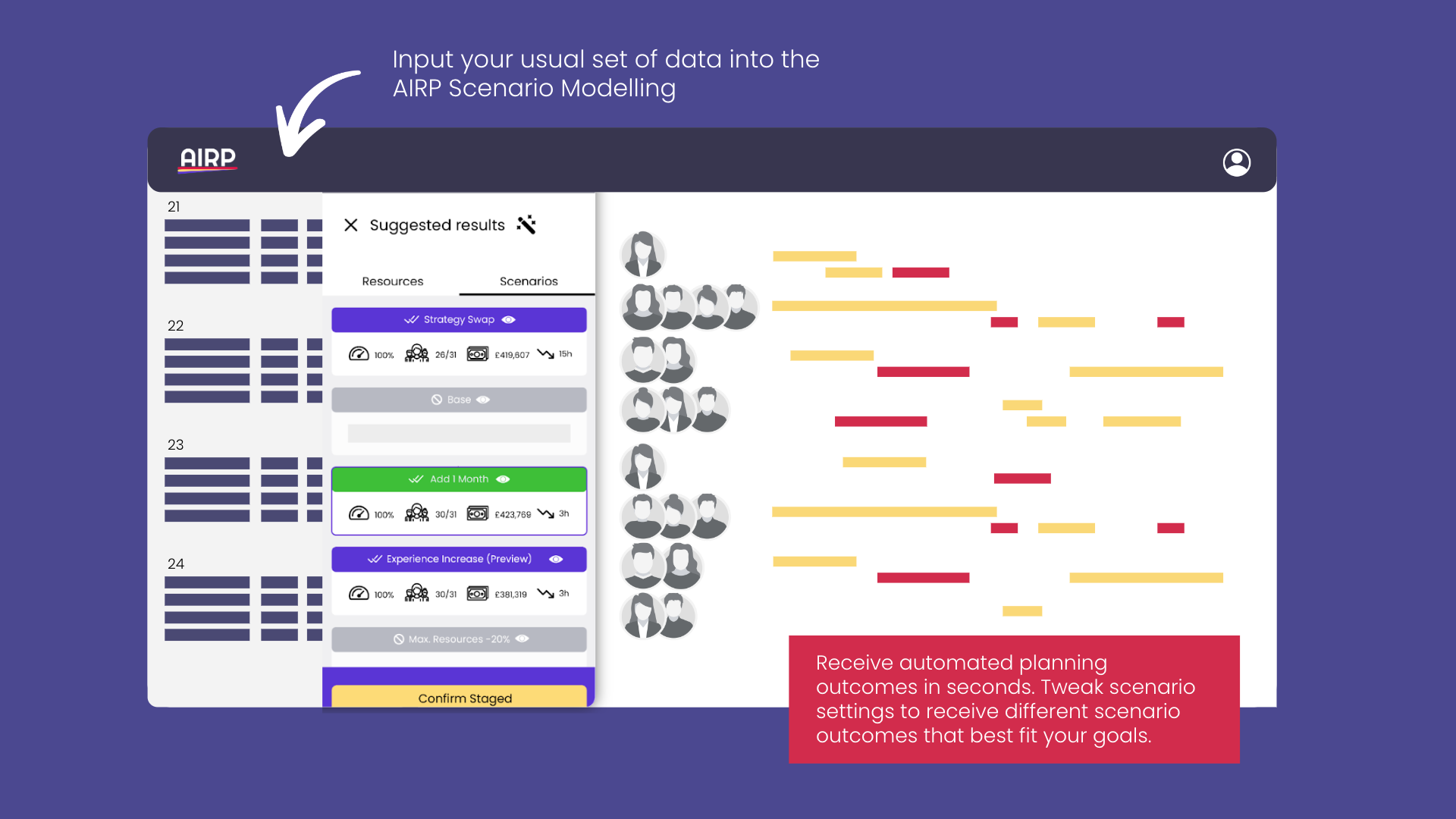
Every scenario produced by AIRP states each resource's pressure maps, is designed to monitor and balancing workload, ensuring that resources are more likely to be allocated efficiently. As a result, manufacturers can quickly re-prioritise their production when needed without relaunching MES estimation or time-consuming Excel re-calculations.
Below is a short list of objectives that are built-in in AIRP:
- Planning by delivery date (soft, hard contracts).
- Plan to optimise turnover constraint.
- Plan to complete the number of hours of holidays and permits.
- Plan to optimise the cost.
- Shifts management.
The shift management enables the organisation smoothly customised the required constraints and the optimisation rules to integrate and just let the AIRP algorithms guide them in discovering the monthly or weekly shift schedule.
Familiar with these challenges? Let's explore your use case!