In the last decade, the industrial scenario, and in particular the manufacturing area, was marked by an evolutionary thrust that influenced the digitalisation process. In the recent years, what is giving the rhythm to the future of manufacturing is defined as IIOT (Industrial Internet of Things), the natural evolution of modern IoT solutions, but with such a disruptive impact to forge the definition of Fourth Industrial Revolution.
The absence of a recognised standard, together with the complexity of an extraordinarily variegated scenario, determines a continuously evolving market. Inside of it, the major cloud providers and many OEMs (Original Equipment Manufacturers) propose their own platforms and their own "standards". In Italy, the initiative "Piano Industria 4.0" aims to digitalise and standardise the manufacturing scenario, interconnecting machines and integrating them inside the company software and processes.
Despite the grants available, the potential of this new paradigma still remains unexpressed, particularly in the world of the SMEs,
where the processes to interconnect systems and gather data are often inexistent or not structured enough.
With these premises, we couldn't let go of the opportunity of widening our expertise on the subject. Therefore, I decided to take part in an international program supported by the European Union, which focused on the new technological trends of the manufacturing area and the IoT platforms for "Industry 4.0". The program ran over two weeks, and it featured many speeches and exciting case history, held by authorities of the field. The event gathered more than fifty people, in between students and young professionals, from all over the world. The objective was one: to prototype new IoT solutions and present them to a jury of professors, start-ups and industrial partners, such as Siemens, BMW and Atos.
The entire experience happened in the suggestive Faculty of Informatics of the Technical Universit (TUM) of Munich, one of the most innovative campuses in Europe. As a start-up incubator, it takes advantage of prestigious collaborations and partners to favour its new projects.

During the experience, we could count on the support of a team of professionals of Futurice, a company working on digital innovation that offers consultancy in project management, in the creation of digital strategies and in the transformation of innovative business models to be "ready for the future".
The people of Futurice guided us in different project phases: analysis of requirements with the stakeholders, designing and conceptualization, definition of the MVP (Minimum Valuable Product), etc. The prototyping was structured following modern paradigms named LSC (Lean Service Creation), that find their roots in the Agile mindset; a process very similar to how we usually work on our projects.
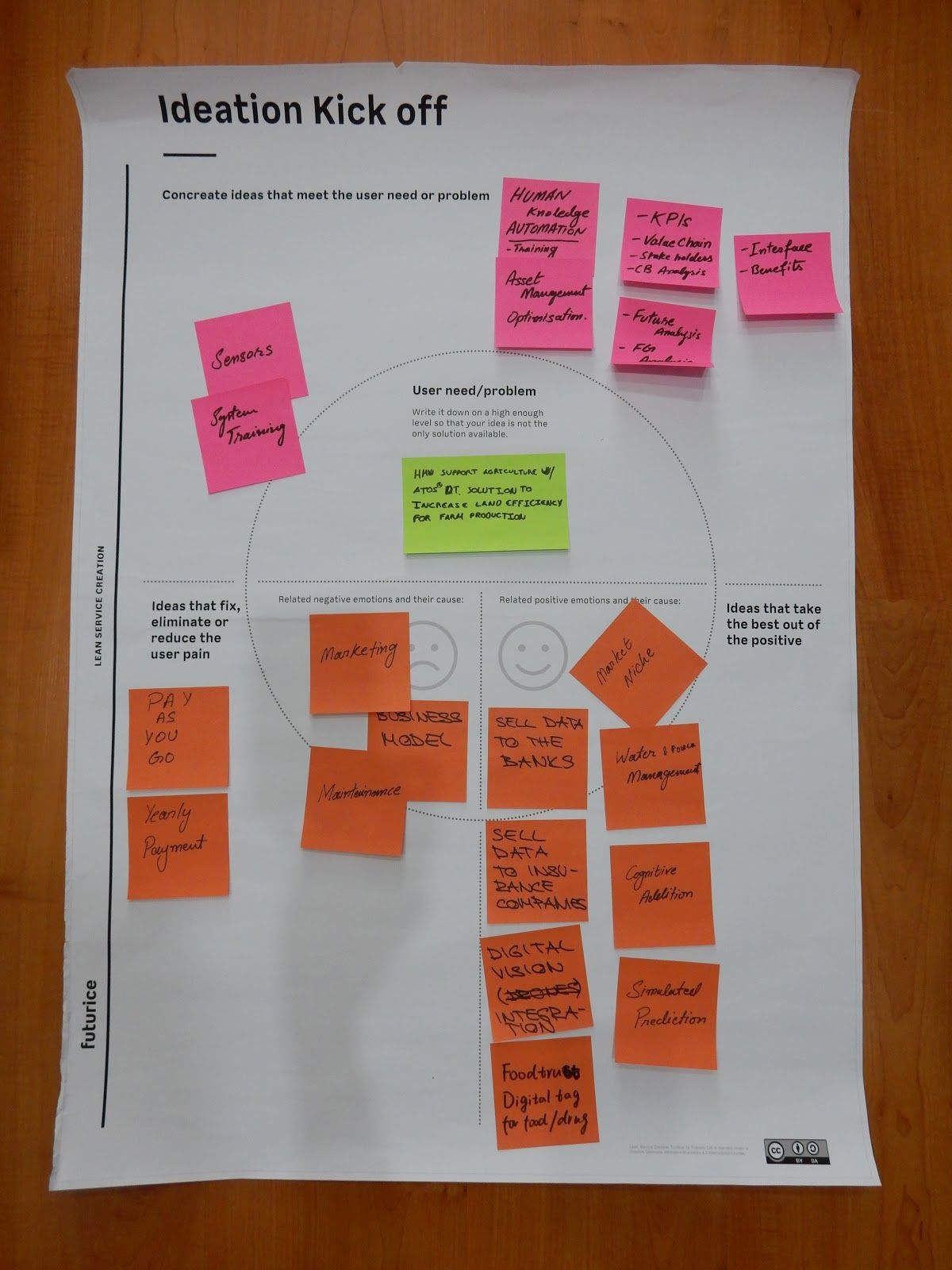
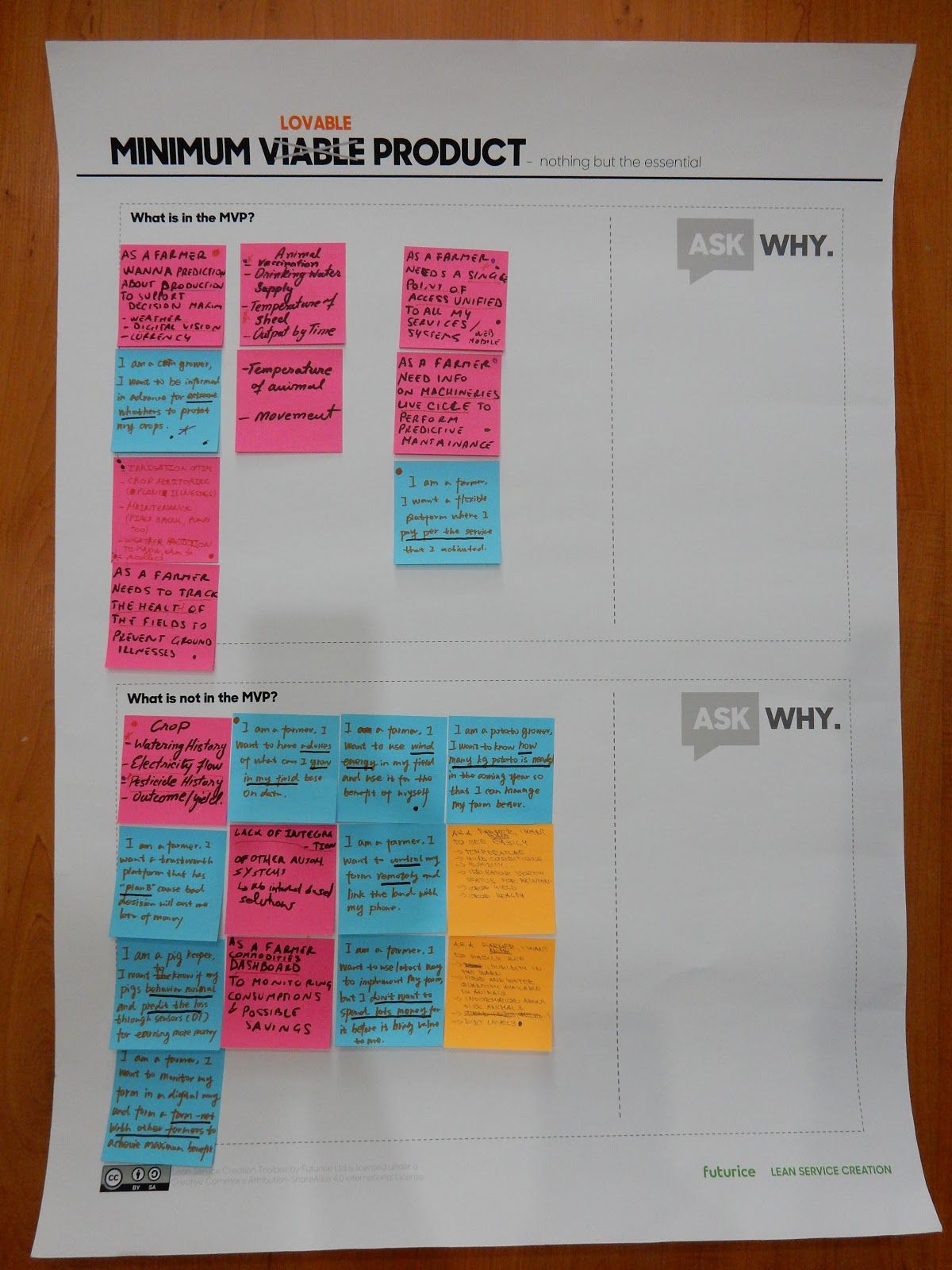
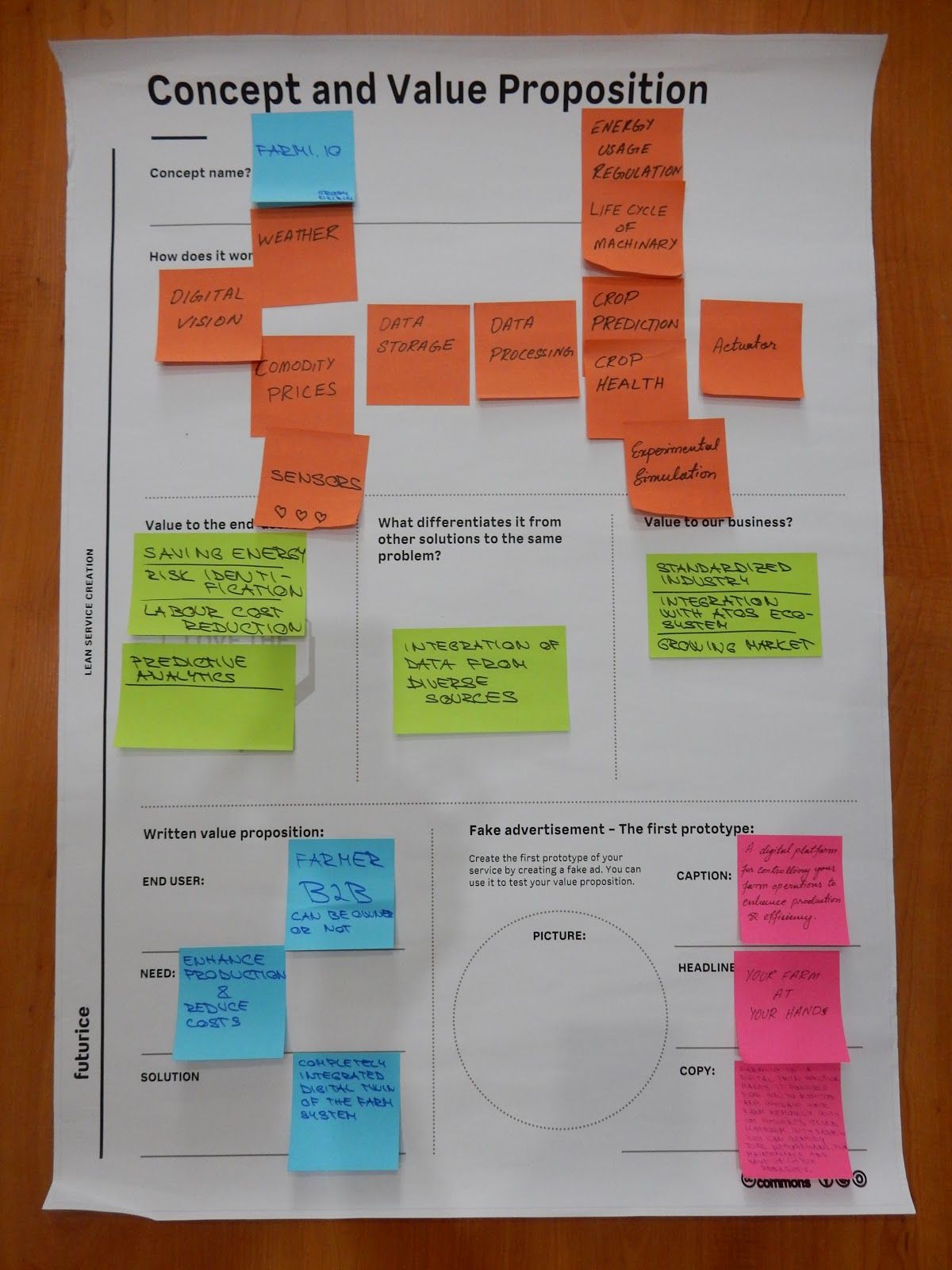
Gathered a cross-functional team, we worked on the prototyping of a new solution to monitor the status of industrial plants and to guarantee the quality of processes that feature many rural and manufacturing realities. The plan was, therefore, to design a distributed system able to communicate, as an add-on, with physical and digital pre-existing systems. By taking advantage of the computational power and connectivity of Edge devices, the generated data is transferred in the cloud, through API interfaces and secure connections.
Finally, we presented the result to an audience of professionals of the field, that offered their contribution and food for thought on our project.
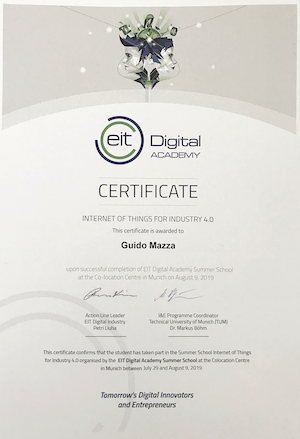
This formative experience gave us new insights on the hot topic of the Fourth Industrial Revolution. Furthermore, it confirmed how the potentiality of cloud infrastructures, API interfaces and mobile apps stand as enabling technologies for the manufacturing field. Many new and sparkling ideas to concretise together with our partners: join us!